Your Guide to Enhancing Safety in Manufacturing
June 13, 2024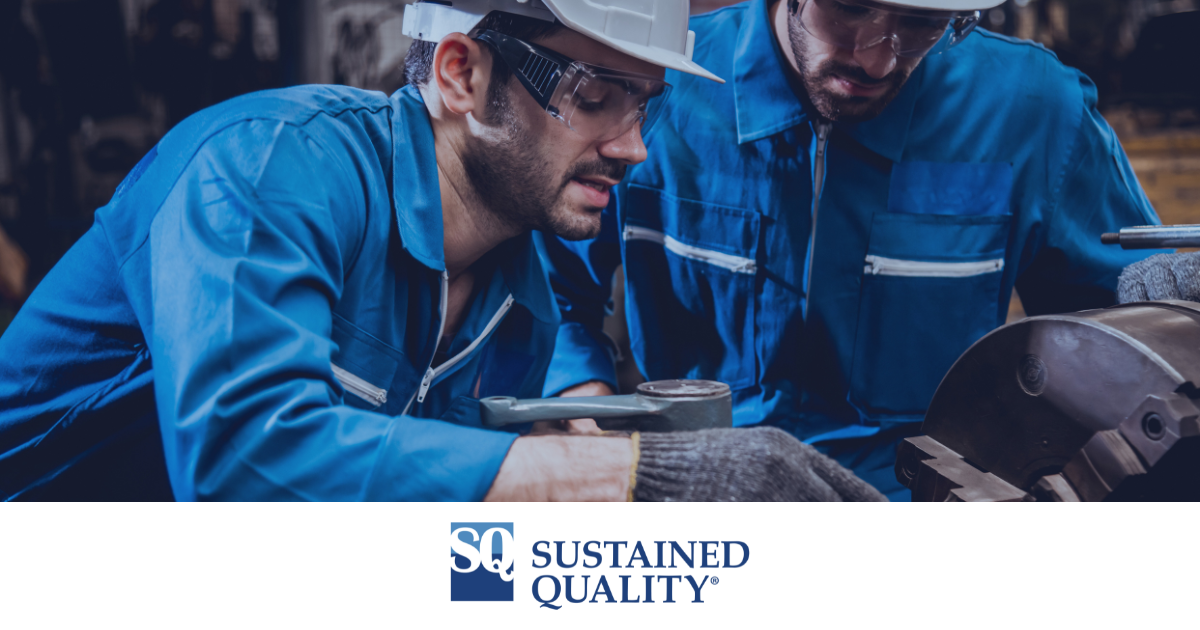
Manufacturing is a cornerstone of our economy. However, it is also a sector fraught with potential hazards, making safety an imperative focus. June is National Safety Month, the perfect time to take a deep dive into this subject.
Ensuring the well-being of workers isn’t just about compliance—it’s about fostering a culture where safety is integrated into every process and decision. This means instilling a collective mindset that prioritizes safety above all else, from the top leadership down to the newest employees on the shop floor.
Essential Areas for Safety Programs
Safety programs must encompass comprehensive approaches and procedures covering several critical areas:
1. Open Communication: Employees should feel comfortable speaking up if they notice a potential hazard or unsafe practice, without fear of retaliation. This can be achieved by creating a culture of trust and transparency within the organization, where employees know that their voices will be heard, and their concerns taken seriously. Reward employees for their commitment to safety. By making safety a core value of your company, you can create an environment where everyone feels empowered to speak up and take action to prevent accidents.
2. Emergency Preparedness and Response: Detailed plans for various emergencies (e.g., fire, chemical spills, natural disasters) including evacuation routes, communication protocols, and roles and responsibilities.
3. Hazardous Materials Management: Procedures for the safe handling, storage, and disposal of hazardous materials, including proper labeling and use of personal protective equipment (PPE).
4. Equipment Safety: Guidelines for the safe operation, maintenance, and inspection of machinery and equipment. This includes Lockout/Tagout (LOTO) procedures and machine guarding.
5. Fall Prevention: Training for correct use of ladders and scaffolding including proper equipment setup. Guidelines for proper footwear. Installation of guard rails, traction enhancements, lighting, and related environmental upgrades.
6. Ergonomics: Strategies to prevent musculoskeletal disorders by designing workstations and tasks that minimize repetitive strain and awkward postures.
7. Training and Education: Ongoing training programs to educate employees about workplace hazards, safe practices, and emergency response.
8. Health and Wellness: Initiatives to promote overall worker health, including hearing conservation, respiratory protection, and programs to address mental health and stress.
9. Incident Investigation and Reporting: Procedures for reporting, investigating, and analyzing workplace incidents to prevent recurrence. This includes root cause analysis and implementation of corrective actions.
10. Personal Protective Equipment (PPE): Clear guidelines on the selection, use, and maintenance of PPE, ensuring that workers are adequately protected based on their specific tasks and environments.
Creating an Effective Safety Playbook
A safety playbook is a comprehensive guide that outlines an organization’s safety policies, procedures, and protocols. Developing a safety playbook begins with conducting a thorough risk assessment to identify potential hazards in the workplace. This involves analyzing all aspects of the manufacturing process, from raw material handling to final product packaging, to pinpoint areas of concern.
Next, it’s essential to establish clear and concise safety policies that comply with OSHA standards and other relevant regulations. These policies should address all identified risks and provide specific guidelines for safe practices. Clarity and specificity are crucial to ensure that everyone in the organization understands the protocols and adheres to them consistently.
Engaging employees in the development of the safety playbook is also vital. Their firsthand experience and insights can be invaluable in identifying potential hazards and practical solutions. When employees are involved, they are more likely to understand and commit to the safety procedures, fostering a culture of safety throughout the organization.
For each identified risk, develop detailed procedures that outline the steps to mitigate the hazard. This includes the use of personal protective equipment (PPE), emergency response actions, and specific operational guidelines. Detailed procedures help ensure that everyone knows exactly what to do in different scenarios, reducing the likelihood of accidents and injuries.
Training and communication are key components of an effective safety playbook. All employees should receive regular training on the safety policies and procedures. Utilizing a variety of methods—such as workshops, drills, and e-learning modules—can help reinforce the information and cater to different learning styles. Ongoing communication ensures that safety remains a priority and that employees are kept informed of any updates or changes.
A safety playbook should be a living document that is regularly reviewed and updated to reflect new hazards, changes in processes, or updates in regulations. Encouraging feedback from employees can lead to continuous improvement of the safety program. This iterative process helps keep the safety protocols relevant and effective.
Finally, it’s important to implement mechanisms to monitor compliance with the safety playbook. This includes regular audits, safety inspections, and performance metrics. Monitoring compliance helps assess the effectiveness of the safety procedures and identify areas that may need adjustment. Using this data to make informed decisions ensures that the safety playbook remains a robust tool for protecting employees and maintaining a safe workplace.
Common OSHA Safety Violations in Manufacturing
The Occupational Safety and Health Administration (OSHA) plays a vital role in regulating workplace safety in the United States. Let’s explore common OSHA violations and critical areas that safety programs must address:
1. Fall Protection (Standard 1926.501): Falls are a leading cause of serious work-related injuries and deaths. OSHA requires employers to provide proper fall protection systems, including guardrails, safety nets, and personal fall arrest systems.
2. Hazard Communication (Standard 1910.1200): Proper labeling and communication about hazardous chemicals are essential. Employers must ensure that all hazardous chemicals are properly labeled, and employees are trained on their risks and safe handling.
3. Scaffolding (Standard 1926.451): Incorrect use or assembly of scaffolding can lead to collapses and falls. OSHA standards require proper design and construction of scaffolds and safe access for workers.
4. Respiratory Protection (Standard 1910.134): When workers are exposed to harmful dust, fumes, or gases, respiratory protection is critical. Employers must provide appropriate respirators and ensure they are properly fitted and maintained.
5. Lockout/Tagout (Standard 1910.147): Lockout/Tagout (LOTO) procedures prevent accidental machine startups during maintenance. Failure to comply with LOTO procedures can result in severe injuries.
6. Powered Industrial Trucks (Standard 1910.178): Forklifts and other powered industrial trucks must be operated safely. OSHA requires proper training and certification for operators and regular equipment inspections.
7. Machine Guarding (Standard 1910.212): Unguarded or inadequately guarded machines pose serious risks. OSHA mandates guards to protect workers from moving parts and other hazards.
8. Eye and Face Protection (Standard 1926.102): In environments where there is a risk of flying debris, chemical splashes, or harmful light radiation, appropriate eye and face protection must be provided and used.
Creating a safe manufacturing environment is an ongoing process that requires commitment, cultural changes, vigilance, and a proactive approach. By addressing critical areas in safety programs, building a culture of safety, and developing a comprehensive safety playbook, manufacturing facilities can protect their most valuable assets—their employees. Emphasizing safety not only ensures compliance but also enhances productivity, morale, and overall success.
Expand your workforce through our production support with highly trained Sustained Quality Associates. Find out more today.