Tools, Methods and Techniques Used In APQP
August 15, 2024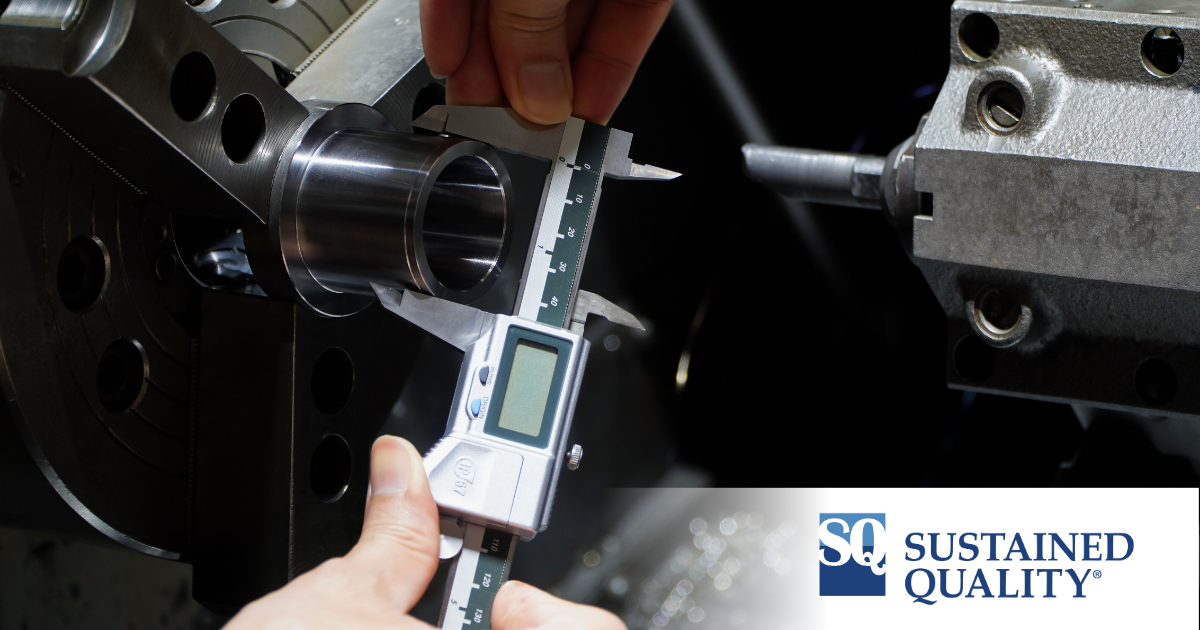
Advanced Product Quality Planning (APQP) is a framework designed by the auto industry consisting of techniques and procedures for the quality development of new products that will satisfy the end-user. There are a multitude of methods that can be incorporated into this framework. Taken together, these tools embed quality control practices into the product development process to achieve the ultimate goal: better products for the customer.
Let’s look at the many available methods that can be used in APQP to help minimize errors and achieve high-quality production results.
Failure Mode and Effects Analysis (FMEA)
FMEA is a detective tool that helps to spot potential problems in the product or process. It helps reveal how bad the problem could be, how often it might happen, and how easily it can be caught. By using FMEA as a quality control tool in APQP, it is simple to tackle issues early on and make sure a product turns out the best that it can be for customers.
Control Plans
Control Plans are detailed documents that outline the steps and processes needed to ensure that a product meets customer requirements. They are like a blueprint for monitoring and controlling the quality of the product throughout the manufacturing process. It helps to draw out guidelines for product quality and actively address any potential issues.
Design of Experiments (DOE)
Design of Experiments (DOE) is a method that helps optimize product design and process parameters by conducting controlled experiments. It allows teams to understand how different variables impact outcomes. From here the teams can make informed decisions to improve quality. Because of this, DOE will lead to higher-quality products for customers.
Statistical Process Control (SPC)
Statistical Process Control (SPC) are machines that keep an eye on process variability. It helps teams identify trends, patterns, and issues in the process so they can take corrective actions. It also helps to maintain quality standards. SPC is a key quality control tool in APQP that ensures processes are stable, predictable, and meet customer requirements. By using SPC in APQP, companies can manage variability and consistently deliver quality products.
Production Part Approval Process (PPAP)
The Production Part Approval Process (PPAP) is the final quality check before mass production. PPAP makes sure everything meets the requirements it needs to set in the control plans. By submitting samples and documentation, companies can make sure that products meet customer specifications and quality standards. PPAP is a great quality control tool in APQP. It is also an essential one in giving companies confidence in their production process and product quality. Incorporating PPAP into APQP helps companies avoid defects.
Measurement System Analysis (MSA)
Measurement System Analysis (MSA) is a method used to assess the reliability and accuracy of measurement systems used in QC processes. By evaluating the measurement systems, MSA helps ensure that any variation in measurements is due to the actual product or process. This means that the measurement system itself is reliable. MSA is being used in APQP to validate the accuracy and consistency of measurements. This helps to ensure that all the products are made with improved product quality and meet customer satisfaction.
Process Flow Diagrams
A process flow diagram is simply a visual representation of the steps in a given process. It shows how information flows work or how materials are used through a series of steps or stages. Process flow diagrams are used in many different industries to help understand and optimize processes. They also help to identify inefficiencies and communicate complex processes to stakeholders. Some common elements found in process flow diagrams include:
- Start and end points: Indicates where the process begins and ends.
- Process steps: Shows the individual steps or tasks in the process, often represented by symbols or shapes like rectangles or circles.
- Decision points: Indicates where a decision needs to be made in the process, often represented by diamond shapes.
- Inputs and outputs: Shows what materials, information, or resources are needed for each step and what is produced as a result.
- Connections: Arrows that show the flow of materials, information, or resources between steps.
By visually mapping out a process flow, organizations can identify bottlenecks, redundancies, and opportunities for improvement. That is how they help to ensure that products meet the needs of customers and that they are high-quality products.
Poka-Yoke
Poka-Yoke is also known as Error Proofing. It is a Japanese term that means mistake-proofing. It involves implementing techniques to prevent errors by designing processes or products in a way that makes mistakes either impossible or easy to find. By incorporating Poka-Yoke techniques, companies can reduce the risk of defects in a product. Poka-Yoke is a valuable quality control tool used in APQP to enhance process efficiency, reduce waste, and ensure that products meet customer requirements. By integrating Poka-Yoke into the APQP process, companies can minimize errors, streamline production processes, and deliver high-quality products to customers consistently. Poka-Yoke techniques help in creating a foolproof system that eliminates human errors.
A few Poka-Yoke techniques include:
- Checklists: Using checklists to ensure all necessary steps are completed in a process and to verify that no steps are missed.
- Warning devices: Using visual or auditory warnings to alert operators of potential errors or issues in the process.
- Jigs and fixtures: Designing tools or fixtures that guide operators to perform tasks properly and prevent errors.
- Color-coding: Using colors to differentiate between parts or components. This makes it easier to identify and prevent mistakes.
- Sensors: Using sensors to detect errors or abnormalities in a process and automatically stop the process. This helps to prevent further mistakes.
- Andon systems: Implementing visual communication systems that signal when an error occurs. This allows operators to quickly address the issue.
- Kaizen (Continuous Improvement): Encouraging a culture of continuous improvement where employees are empowered to identify and implement solutions.
5 Whys Analysis
The 5 Whys Analysis is a problem-solving technique that involves asking “why?”’ over and over to get to the root cause of an issue. By digging deeper and asking multiple whys, teams can uncover underlying issues and address them effectively. The 5 Whys Analysis is a valuable tool used in APQP to identify and resolve problems early in the product development process. By using the 5 Whys Analysis in APQP, companies can improve product quality, and identify recurring issues. It is used to make informed decisions to prevent similar problems in the future. This structured approach helps teams address the root causes of issues rather than just treating symptoms. In turn, this leads to long-term solutions and continuous improvement.
As you can see, there are plenty of APQP tools out there. Incorporating APQP tools and techniques like FMEA, control plans, and process flow diagrams into your projects can give you peace of mind. It helps you ensure that the products you deliver are of the highest quality. If you need help with your quality assurance processes, reach out to Sustained Quality.