The Baby Boomer Exodus: Implications for the Automotive Manufacturing Workforce
October 16, 2024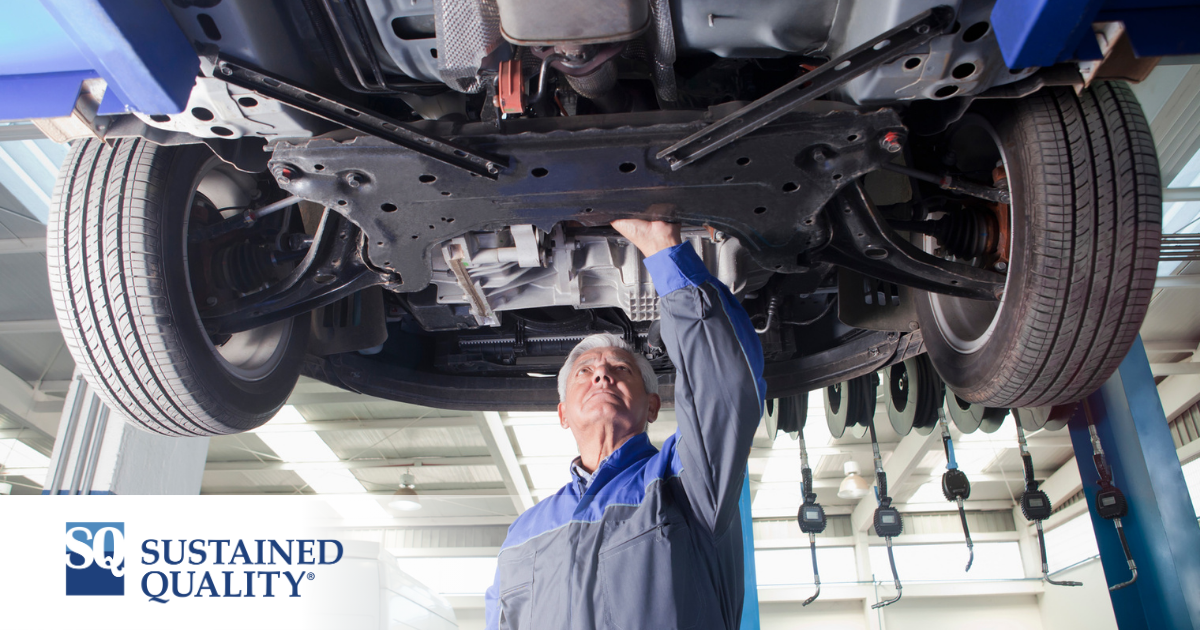
As the Baby Boomer generation reaches retirement age, industries across the board are bracing for significant workforce changes. This demographic shift is particularly impactful in sectors like automotive manufacturing, where experience and expertise play crucial roles in maintaining ambitious standards of quality and efficiency. This change poses challenges in recruiting, hiring, and retaining skilled workers, as well as maintaining the quality of the products. Companies must take proactive steps to address these changes to avoid potential quality issues and increased costs.
The Impact of Baby Boomer Retirements
One of the most immediate challenges automotive manufacturers confront is that the departure of seasoned workers means losing decades of accumulated knowledge and hands-on experience. This can negatively impact the quality and consistency of automotive manufacturing. New hires, no matter how well-educated, cannot immediately replicate the proficiency of a veteran worker with 20+ years of experience. This gap can result in increased error rates, production delays, and potentially higher costs associated with quality control and rework.
Another significant problem is the recruitment of new talent to replace retiring Baby Boomers. The automotive industry, traditionally seen as labor-intensive and requiring specialized skills, has struggled to attract younger generations. Millennials and Gen Z often gravitate towards tech-driven industries, perceiving them as more innovative and aligned with modern work-life balance preferences.
Addressing the Knowledge Gap and Attracting New Workers
A robust plan must include comprehensive strategies aimed at capturing and transferring the knowledge of retiring workers to new employees and training methods to complement this. Additionally, it must implement policies that effectively draw potential new hires to the industry. Improving appeal could mean updating job roles that align more closely with current expectations regarding job culture.
First, let’s examine methods to transfer historical knowledge and accelerate the training of new employees.
Knowledge Transfer Programs. Developing structured knowledge transfer programs is essential. This can involve mentorship schemes where retiring employees are paired with new hires to facilitate hands-on training and knowledge sharing. Detailed documentation, video tutorials, and best practice guides can help to transfer critical skills and insights from veterans to rookies.
Succession Planning. Effective succession planning ensures that there is always a pool of trained and capable employees ready to step into key roles. This involves identifying potential leaders within the organization and providing them with the necessary training and development opportunities to prepare them for future responsibilities. Additionally, succession planning should include rotational programs that expose these future leaders to different aspects of the business, thereby broadening their experience and understanding of the company’s operations. This integrated approach not only prepares individuals for leadership roles but also ensures they are well-versed in various functions, fostering a more adaptable and resilient leadership team.
Continuous Training and Development. Investing in continuous training programs helps new employees develop their skills more rapidly. Leveraging modern technologies like virtual reality (VR) and augmented reality (AR) can enhance training efficiency and engagement. These tools can simulate real-world scenarios, allowing new hires to practice and refine their skills in a controlled environment. For example, General Motors (GM) has been actively investing in training programs to upskill its workforce and prepare for the future. They have partnered with educational institutions to create apprenticeship programs that provide hands-on experience and mentorship from seasoned professionals.
Partnerships with Educational Institutions. Collaborating with technical schools, colleges, and universities can help create a pipeline of skilled workers tailored to the specific needs of the automotive industry. These partnerships can involve internships, co-op programs, and specialized training courses designed to equip students with the skills required for modern manufacturing roles.
Embracing Technology and Automation. Automation and advanced manufacturing technologies can help bridge the gap caused by retiring workers. By integrating robotics, AI, and machine learning into production lines, companies can enhance precision, reduce error rates, and maintain high-quality standards with a smaller, less experienced workforce. While this doesn’t replace the need for skilled human workers, it complements their efforts and alleviates some of the pressures.
Implementing Advanced Technologies. Younger generations who have grown up in a tech-heavy environment are comfortable working in environments that leverage modern technologies. By integrating advanced manufacturing technologies, such as automation, AI, and machine learning, automotive companies can create a dynamic and forward-thinking work environment. These tools improve operational efficiency and tend to align with the interests and skills of younger employees.
Now let’s look at ways to redefine and enhance the work culture and reputation of the automotive manufacturing industry to improve hiring success and reduce turnover. Retaining younger employees in the automotive manufacturing sector requires creating a work environment that meets their needs and expectations. The industry’s demanding nature, combined with the steep learning curve, can lead to high turnover rates among younger employees. To mitigate this, companies can offer competitive compensation, benefits, and career advancement opportunities while fostering a culture of innovation and inclusivity.
Competitive Salaries and Benefits. Offering competitive salaries is fundamental in getting and retaining talent; this is certainly not new news. Still, automotive companies must regularly benchmark their salary offerings against industry standards to ensure they remain relevant. Beyond salaries, comprehensive benefits packages are crucial. These should include health insurance, retirement plans, paid time off, and wellness programs. Providing these benefits not only attracts employees but also demonstrates a commitment to their well-being and long-term stability.
Career Growth. Younger employees seek clear career progression opportunities. Establishing well-defined career pathways, with transparent criteria for promotions and advancements, helps employees understand their potential for growth within the company. Regular performance reviews and feedback can guide employees on how to achieve their career goals.
Work-Life Balance Policies. Supporting a healthy work-life balance is essential for retaining younger employees. Adopting flexible work arrangements, such as remote work options for certain roles or flexible shift patterns, can make the industry more inviting to younger workers who prioritize work-life balance. Encouraging employees to take time off when needed helps prevent burnout and promotes long-term job satisfaction. This approach can also help retain older workers who may wish to transition to part-time roles rather than full retirement.
Employee Input. A culture that encourages creativity and innovation can significantly enhance job satisfaction among younger employees. This involves creating an environment where new ideas are welcomed, and employees are encouraged to offer feedback. Companies can establish innovation labs or dedicate time to brainstorming sessions to foster this culture.
Toyota, for instance, has implemented various initiatives to create a more inclusive and engaging workplace. They focus on continuous improvement and encourage employees at all levels to contribute ideas for innovation. This method keeps employees motivated and ensures a steady stream of improvements in their manufacturing process.
Recognition. Recognition and reward programs to recognize and reward employees for their contributions are crucial. This can be through formal programs like employee of the month awards, or informal acknowledgments such as shout-outs in meetings. Recognizing achievements boosts morale and motivates employees to continue performing at their best.
Long-Term Benefits of Proactive Measures. By proactively addressing the impending retirements of Baby Boomers, automotive manufacturers can ensure a smoother transition and maintain high standards of quality and efficiency. A well-trained and engaged workforce directly contributes to maintaining product quality. A workforce that combines the experience of older employees with the fresh perspectives of younger workers can drive innovation. This blend of skills and ideas can lead to the development of new manufacturing techniques, improved products, and a competitive edge in the market.
The retirement of Baby Boomers represents a significant shift in the automotive manufacturing workforce, bringing both challenges and opportunities. Companies that recognize and address these changes proactively will be better positioned to maintain high standards of quality, recruit and retain skilled workers, and foster innovation. Through strategic knowledge transfer, continuous training, and the integration of advanced technologies, the automotive industry can navigate this transition successfully and continue to thrive in a rapidly evolving landscape. Let Sustained Quality help keep your operations running smoothly and on track.