Quality Services
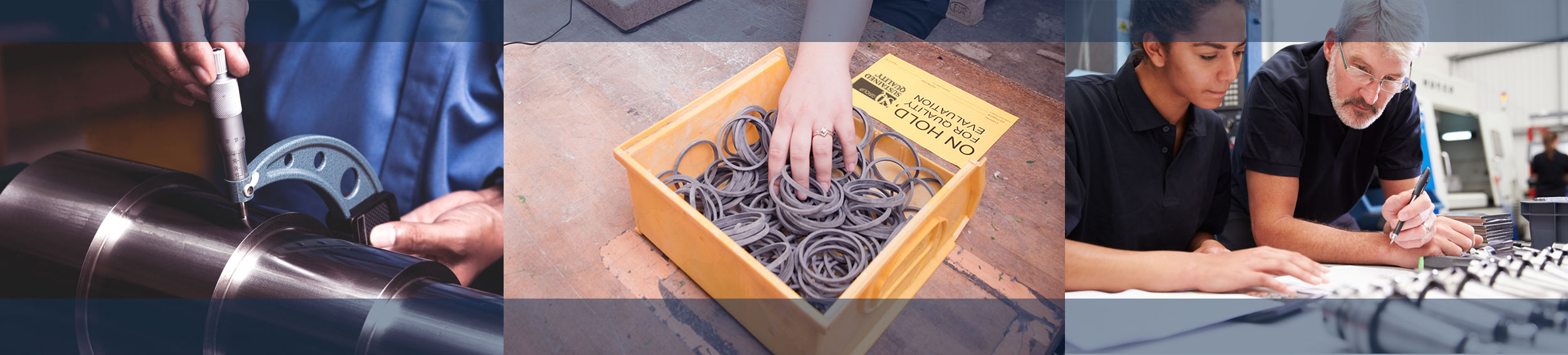
Sustained Quality prevents mistakes or defects in manufactured products and avoids problems when delivering solutions or services to customers; defined by ISO 9001 as “part of quality management focused on providing confidence that quality requirements will be fulfilled”.
- Launch Support/GP-12/Quality Wall
We manage products improving readiness and process to prevent post-production issues. - Rework/Sorting
We process and arrange parts according to sequence/set or rectify mistakes made during manufacturing so that a product meets requirements. - Level 2 Containment
We eliminate Hazard Level 2 parts, ensuring no defected or nonconforming parts are released. - Off-Site Inspection
We visually analysis and report part defects at customer facilities during production or in warehouse. - Quality and Safety Training
We conduct off-site or on-site training designed to teach processes to maintain quality and occupational, safety and health standards developed by the United States government’s OSHA organization.
SQ provides specialty trained associates to protect the customer from any nonconforming parts. Our team is responsive, on-time and has strong leadership to follow standardized work that is validated through our layered audits.
100% part conformance saves money by reducing rework, production delays, and warranty claims. SQ provides a documented and systematic process that ensures conforming products reach the customer and defects are contained.
- Set Up – Established project management techniques are applied to each job
- Training – Employees are trained and supervised by experienced Sustained Quality managers
- Control – Stringent controls maintain integrity in each step of the process
- Reporting – Detailed reports provide customers with up-to-date results
- Layered Audits – Inspection process audit to review general set up, work instructions, tools and gauges, product identification, work area and documentation
- Invoicing – Customer invoices are completely transparent with name of inspector, bill rate and hours worked on that particular project
- Improvement – Sustained Quality management reviews and implements dozens of improvement ideas from our team each year to improve our level of quality and service
Containment
A core competency of Sustained Quality is the ability to successfully execute inspection and containment projects. SQ mobilizes rapidly and establishes control of the parts in question. After establishing the quality gate, SQ inspectors perform their tasks according to detailed and documented work instructions. Data pertaining to the parts inspected is gathered and reported in an effort to drive to root cause and corrective action.