Promoting a Culture of Continuous Improvement
July 25, 2018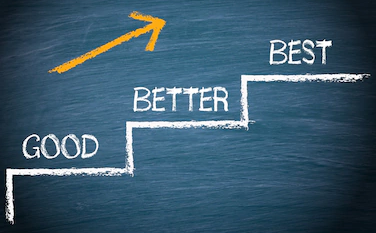
It is common to talk about quality and continuous improvement in the context of manufacturing.
Methodologies such as ISO, lean and Lean Six Sigma are a means to improve business efficiency and effectiveness. When done well, the end result is a better experience for customers and employees, and bottom-line benefits to the organization.
But continuous improvement is no longer captive to these existing frameworks or to manufacturing. It is now found everywhere and industry-blind.
“Continuous improvement is simply about the people and processes that make up a business,” says Samantha Kaplan, director of quality and continuous improvement at Corporate College, a division of Cuyahoga Community College. “It’s becoming part of the culture and put in practice at every level of an organization.”
Below are responses from Kaplan when asked about how quality and continuous improvement affects organizations, regardless of sector.
Where are quality and continuous improvement processes found today?
This initiative can be in any organization. The methodologies typically had been applied to specific industries, such as ISO in manufacturing, particularly automotive, medical devices and aerospace, but these ideas have made their way into other industries.
Generally, however, many organizations are implementing a culture of continuous improvement. They are regularly looking at processes to see where and how improvements can be made. In some cases, performance can be measured against metrics.
In some industries, continuous improvement drives funding. How well they are able to meet measurables is directly tied to their funding. Elsewhere, it is about being more effective and efficient.
Improving processes requires that problems are identified, action is taken to fix them, there are checks to see the results of that action and the process is reviewed to see how it can be done better. It first requires a commitment to a culture of improvement; then the best tools and techniques can be identified for that organization.
Ultimately, organizations can not accept status quo. They need to improve and streamline to remain competitive.
What difference does such a process make for an organization?
Continuous improvement affects how an organization operates. It becomes natural to make improvements, correct problems to be more efficient and effective, rather than being reactive. It also creates a culture of problem solving — dedicating time to get to the bottom of issues and fix the problem.
There is a direct link to the strategic vision of an organization. It is carried out not just from the top down, but simultaneously from the bottom up so that the entire organization is committed to the same idea.
How can organizations ensure their process improvement initiatives stick?
It requires a commitment. It is essentially a strategic initiative, so it needs to be reinforced from the top and by champions throughout the organization.
Recently, ISO standards have been revised to focus more on leadership’s role in process improvement, as well as providing resources and assigning responsibility. There has to be accountability and encouragement to think creatively when problem solving. Then it becomes more of an organizational management system and not simply a quality management system.
Continuous improvement must be embedded in the organization’s DNA. The strategic vision should reflect this, so there’s a commitment to improvement, which can be leveraged in many ways.
Sometimes that requires stepping back and taking a high-level look to find where the organization can be more effective and efficient in how it meets the needs of customers and improves performance metrics. The commitment to continuous improvement is no longer a discipline strictly for manufacturers.
Burrough, Adam. (2018). “Every organization should promote a culture of continuous improvement”. Retrieved from http://www.sbnonline.com/article/every-organization-should-promote-a-culture-of-continuous-improvement/.