Onsite Supplier Representation for Quality Services in the Auto Industry: Eyes and Ears on the Manufacturing Floor
September 26, 2024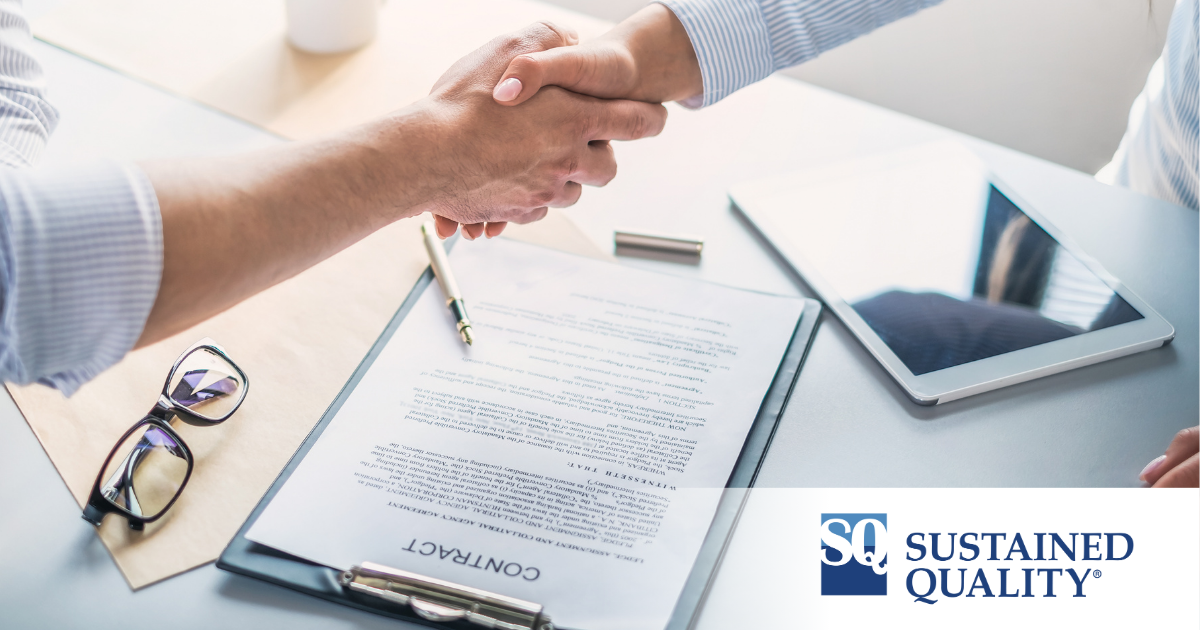
In automotive manufacturing, quality is non-negotiable. Every part, component, and process must meet rigorous standards to ensure the vehicles on the road are safe, reliable, and high-performing. With numerous suppliers contributing to the complex assembly of an automobile, maintaining high quality across the supply chain becomes a formidable challenge. This is where onsite supplier representation plays a critical role in ensuring success.
An onsite supplier representative serves as the supplier’s eyes and ears on the manufacturing floor, ensuring that the supplier is consistently meeting the client’s quality standards. Let’s delve into the benefits of having an onsite supplier representative for quality services, the oversight they provide, and how they serve as a critical liaison between the client and the supplier.
The Importance of Quality in Automotive Manufacturing
A single defective part in a vehicle can lead to safety risks, costly recalls, and damage to the manufacturer’s reputation. The automotive industry faces intense scrutiny, and quality control is paramount throughout the supply chain.
With increasing regulatory standards and customer expectations, manufacturers must maintain strict quality protocols at every stage, from raw material procurement to the final assembly line. While suppliers are integral to this process, managing and monitoring them is complex. That’s where an onsite supplier representative comes in, ensuring that quality expectations are not only communicated but also continuously met on the shop floor.
What Is Onsite Supplier Representation?
An onsite supplier representative is an individual or team stationed at the client’s manufacturing facility to oversee the production of parts or services on behalf of the client. In the case of quality services, this representative is responsible for ensuring that the supplier adheres to the client’s quality standards, performs inspections, and addresses any issues in real time.
In automotive manufacturing, suppliers produce components such as engines, transmissions, or specialized electronics that are crucial to the final product. These components must meet stringent quality specifications to avoid delays or defects in the assembly line. By having a supplier representative on-site, the client can ensure immediate quality checks and proactive issue resolution.
The Role of the Onsite Supplier Representative and the Benefits They Bring
One of the core functions of an onsite supplier representative is providing consistent oversight on behalf of the supplier. Their role goes beyond occasional audits or assessments; they are fully embedded within the client’s manufacturing environment and serve as an extension of the supplier’s quality team. Here are some key responsibilities that supplier representatives for quality services typically manage:
1. Daily Inspections and Quality Audits
Supplier representatives conduct daily inspections and audits of parts being produced. This ensures that any defects or discrepancies are caught early in the production process. These quality checks can range from visual inspections to more sophisticated testing, depending on the complexity of the component. The goal is to identify potential issues before they become larger problems that impact the supply chain.
With a dedicated representative on the ground, manufacturers can have greater confidence that the parts they receive from suppliers meet their high standards. Regular inspections and quality audits reduce the risk of defective components making their way to the assembly line.
2. Monitoring Compliance with Quality Standards
Every automotive manufacturer has specific quality standards that their suppliers must meet. The onsite supplier representative ensures that the supplier consistently complies with these standards. If the supplier deviates from the required quality protocols, the representative can immediately flag the issue and work with the supplier to implement corrective actions.
3. Real-time Problem Solving
Manufacturing is a dynamic process, and issues can arise at any time. Having a supplier representative on-site means that problems can be addressed immediately. If a defect is detected, the representative works with both the supplier and the client’s quality team to resolve the issue on the spot. This real-time problem-solving approach minimizes downtime and reduces the likelihood of defective parts being shipped to the manufacturer. This process reduces delays and keeps the production line running smoothly.
4. Process Improvement and Risk Mitigation
In a highly regulated industry like automotive manufacturing, managing risk is critical. Supplier representatives are not only focused on identifying defects but also on preventing them. By being present on the production floor, they can provide valuable insights into how processes can be improved to reduce the risk of quality issues. This proactive approach helps the supplier and client continuously enhance the production process, leading to higher-quality components and fewer disruptions.
5. Facilitating Communication Between Client and Supplier
Clear communication is essential to maintaining quality in automotive manufacturing. Supplier representatives serve as a direct line of communication between the supplier and the client. They relay any concerns, updates, or requests from the client to the supplier in real-time. This helps to streamline the collaboration process, reduce misunderstandings, and ensure that both parties are aligned on quality expectations.
By working together to address quality concerns and improve processes, both parties benefit from a more transparent and productive relationship. This can lead to long-term partnerships and better overall performance in the supply chain.
The Eyes and Ears on the Manufacturing Floor
In the automotive industry, the stakes for quality control are higher than ever. By investing in onsite supplier representation, automotive manufacturers can enhance their quality assurance processes, mitigate risks, and ultimately deliver safer and more reliable vehicles to their customers. The value of having a dedicated advocate for quality at the supplier’s facility cannot be overstated—it’s a strategic move that pays dividends in both the short and long term.
Businesses looking to optimize their operations can greatly benefit from the expertise and support provided by onsite supplier representatives. Contact us to learn more about how Sustained Quality can help your manufacturing business.