Automakers Take on Larger Role in Testing and Simulation
October 08, 2018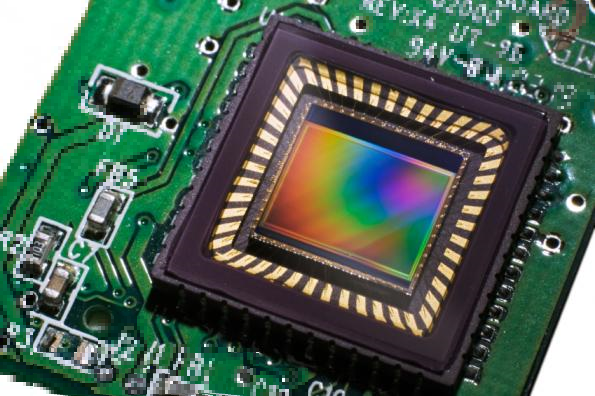
Chip and Electronic Design Automation (EDA) companies are scrambling to deal with stiff safety regulations and harsh environmental conditions for automotive chips, but automakers are making big changes of their own to ensure all those components work together as expected.
The result is a significant shift of responsibilities of companies in the automotive supply chain. Car makers traditionally have left verification, validation and testing of chips and subsystems to their suppliers. In years past, it was enough for those companies—chip makers and Tier 1 and Tier 2 suppliers—to certify that every component they deliver complied with required safety standards and could inter-operate well enough to be plugged in with no further testing. But as the amount of electronic content increases and the complexity of these systems grows, not to mention the deployment of these devices in safety-critical systems, car makers are taking on a much bigger role to ensure these components work in the context of other systems.
There are several key trends driving these changes. Among them:
- Complexity is rising significantly. Testing those systems independently is no longer sufficient, and automakers are in the best position to verify that all of the pieces work together.
- The cost of errors and defects in assisted and autonomous could dwarf issues that have caused costly recalls in the past, particularly as technology takes growing responsibility for on-road maneuvering.
- The automotive supply chain currently is divided into chip makers and suppliers with limited experience in advanced semiconductor technology, and leading-edge semiconductor companies with limited experience in the automotive world.
While car makers can help guarantee the integration of all of those pieces work, they are on a steep learning curve, as well. This is brand new technology, and there are almost certain to be some unexpected speed bumps along the way.
Dealing with Problems in Context
Moving data quickly and efficiently has been a core focus for semiconductor companies. But moving enormous amounts of data being generated by automotive sensors is both inefficient and time-consuming, and that will become more obvious as automakers push to higher levels of autonomy.
That means more data has to be processed and sorted from what is critical, what is important but not time-sensitive, and what is considered useless.
For chip makers and Tier 1/2 suppliers, this means verifying chips that manage wireless communications protocols will perform as advertised without interruptions from such factors as electromagnetic interference or other types of noise. And for car makers, it means putting all of the pieces in place to be able to figure out what can go wrong.
After nearly a century of mechanical engineering, car makers now are being pulled deep into advanced electronics. This marks an enormous shift in car makers’ responsibility, which subcontracted verification, validation and testing to their supply chain in the past.

Fig. 1: Automotive electronics cost as a percentage of total car cost worldwide, 1950 to 2030. Source: Statista
Simulation and ADAS Testing
Testing is essential in assisted and autonomous vehicles. Road testing is still considered essential, but it is also limited. While some companies claim to have millions of miles of real-world testing, some experts say it will take billions of miles before there is enough data to standardize on what works and what does not.
In the meantime, the best solution is more simulation and modeling. The key is making sure that all of the electronics in a car will be robust enough to handle stresses from extreme heat and cold and vibration, as well as dealing with electromigration and other electrostatic effects with circuits that may be “on” for extended periods of time. This is particularly complicated in the autonomous vehicle world because chips are both analog and digital.
Automotive is expected to be one of the big drivers projected for test equipment over the next few years. Frost & Sullivan estimates the global market for electronic test equipment, now at about 150 companies that generated $10.8 billion during 2017, will rise to $13.16 billion by 2022, growing at 4% CAGR on average.
Simulation is expected to benefit, as well. All of the major EDA companies offer a range of simulation tools and services for highly automated vehicles.
Conclusion
The changes in the automotive supply chain are just the beginning. The challenges in this part of the market are so new that it is hard to predict how far the pendulum will swing for automakers taking on a larger role. In the past, car makers would not have to go to such lengths to build their own physical/digital testing environment.
But it is also not a simple process to automate. Using approaches such as a digital twin and simulation-based system integration are still too new in the automotive world to have well-established best practices or easy-to-use tools to build the models and test processes.
Fogarty, Kevin. (2018). “Automakers Take On More Responsibility”. Retrieved from https://semiengineering.com/automakers-take-on-more-responsibility/.