Anatomy of a Safe Launch: A Comprehensive Breakdown
February 18, 2025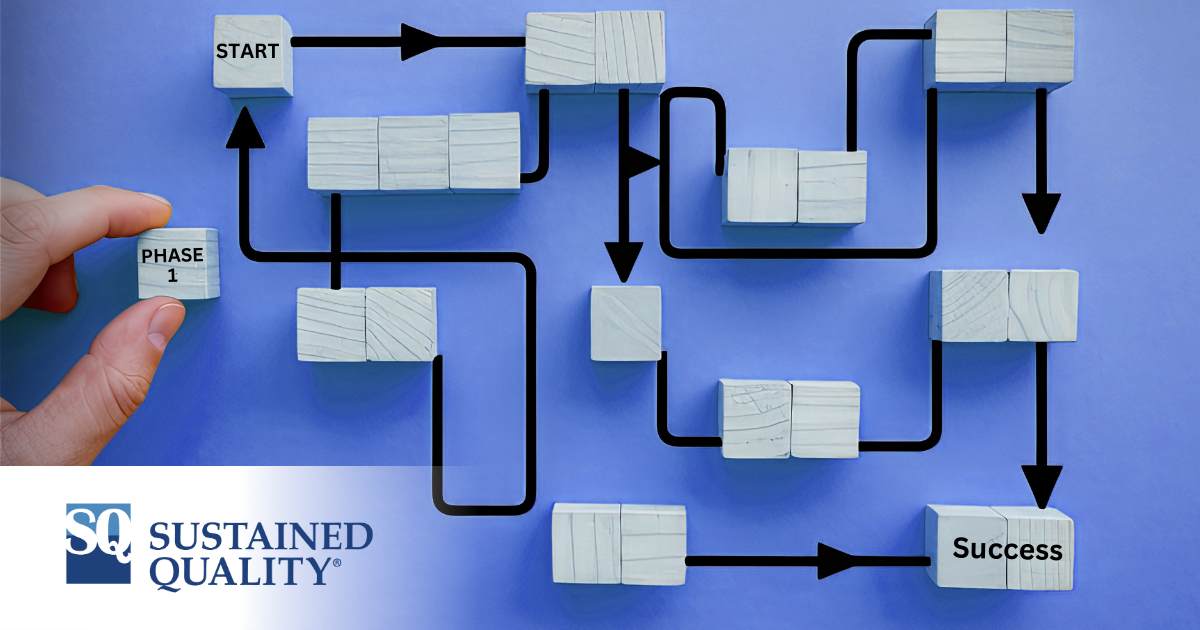
In automotive manufacturing, a safe launch refers to a systematic process implemented to minimize risks and defects when introducing a new product, process, or supplier into production. It’s a key part of the quality process, aimed at ensuring the smooth ramp-up of production and delivering high-quality products from the outset.
One of the most significant advantages of a safe launch is its ability to prevent defects from reaching customers. Enhanced oversight and additional quality checks help manufacturers identify and resolve issues early, reducing the risk of costly recalls or warranty claims. This focus on quality bolsters the manufacturer’s reputation for reliability and excellence.
Safe launches also build trust with Original Equipment Manufacturers (OEMs) and end customers by demonstrating a commitment to meeting or exceeding expectations. By avoiding disruptions and ensuring consistent quality, manufacturers strengthen relationships with key stakeholders in the supply chain.
A successful safe launch involves more than internal processes; it requires collaboration with suppliers to meet quality and delivery standards. By establishing clear expectations and providing support, manufacturers foster partnerships that ensure consistent reliability throughout the supply chain.
Although safe launches require upfront investment in monitoring and containment, they yield long-term benefits. Early detection of defects reduces rework, production stoppages, and downstream issues, leading to significant cost savings and improved operational efficiency.
Real-World Applications in Automotive
Safe launches are particularly critical in:
- New Vehicle Programs: Launching a new model or redesign requires careful quality oversight to ensure that new components and processes function as intended.
- Supplier Changes: When transitioning to a new supplier for critical parts, a safe launch minimizes risks of substandard quality.
- Process Updates: Introducing a new production method or automation system requires validation to ensure it integrates seamlessly into existing operations.
- Product Recalls or Reintroductions: When reintroducing a product after a recall or addressing a known issue, a safe launch ensures the defect has been fully resolved and the product meets quality standards.
- Geographic Expansions: Launching production at a new facility or expanding into a new region requires careful oversight to align with global quality and delivery expectations.
- Pilot Production Runs: Early-stage production of a new model or component benefits from enhanced monitoring to address potential design or process flaws before full-scale production.
- Supply Chain Disruptions: In response to material shortages or supplier disruptions, safe launches help ensure alternative parts or sources meet quality and performance standards.
- Compliance with New Regulations: Implementing changes to meet updated safety or environmental regulations requires thorough testing to avoid non-compliance and associated penalties.
Key Features of a Safe Launch
Enhanced Oversight
A safe launch involves increased monitoring and quality checks during the early stages of production or the introduction of a new product. These measures often include higher inspection rates or additional containment steps to catch defects before they reach the customer. Issues that can be identified and resolved early reduce the risk of broader quality problems later in the process.
Proactive Risk Mitigation
Proactive risk mitigation is a cornerstone of a safe launch. Manufacturers use tools like Failure Mode and Effects Analysis (FMEA) to identify potential failure points in advance. By implementing controls and corrective actions early, risks are addressed before full production begins, safeguarding both the production line and the end product’s quality.
Cross-Functional Collaboration
The success of a safe launch relies on the cooperation of various teams, including engineering, quality assurance, production, and supply chain management. Cross-functional collaboration ensures that all aspects of the launch are aligned, enabling smooth transitions and minimizing the likelihood of miscommunication or overlooked issues. This holistic approach enhances overall launch effectiveness.
Supplier Engagement
Suppliers are integral to the safe launch process so ensuring that suppliers are fully prepared to meet quality and delivery expectations is essential. Supplier engagement often includes joint reviews, audits, and safe-launch protocols for critical components. This collaboration strengthens quality and reliability across the supply chain.
Time-Bound Approach
Safe launches are typically conducted over a defined period, such as the first few months of production. During this time, performance metrics are closely monitored to ensure that processes are running as intended. Once these metrics are consistently met, production transitions back to standard operating procedures. The time-bound nature ensures that quality and operational performance are validated before full-scale production.
Steps in a Safe Launch Process
- Planning and Preparation: Setting the Stage for Success
- Define objectives, timelines, and critical quality parameters.
- Align internal teams on goals and deliverables.
- Pre-Production Validation: Testing the Waters
- Conduct pilot runs or low-volume production to test equipment, processes, and materials.
- Validate tooling, fixtures, and workflows.
- Controlled Production Ramp-Up: Gradually Increasing the Pace
- Gradually increase production volume while closely monitoring quality metrics.
- Track key performance indicators (KPIs) to ensure smooth operations.
- Containment Protocols: Preventing Risks at Early Stages
- Separate and inspect suspect parts before they proceed to the next stage or leave the facility.
- Apply heightened inspection levels (e.g., 100% inspection on critical parts).
- Feedback Loops and Adjustments: Continuous Improvement
- Analyze data from inspections and tests to identify trends or recurring issues.
- Implement corrective actions in real-time.
- Supplier Readiness and Engagement: Finalizing Preparations
- Ensure suppliers meet quality and delivery expectations through audits and joint reviews.
- Collaborate with suppliers to establish safe-launch protocols for critical components.
- Cross-Functional Collaboration: Alignment Across Teams
- Foster communication between engineering, production, quality, and supply chain teams.
- Ensure that all departments are aligned on objectives and procedures.
- Post-Launch Review: Evaluating Success and Areas for Improvement
- Conduct a review to assess the launch’s success and identify areas for improvement.
- Share lessons learned with teams for continuous enhancement in future launches.
A safe launch is a critical investment in the long-term success of automotive manufacturing. By ensuring quality from the start, reducing risks, and strengthening supplier relationships, manufacturers set themselves up for smooth production ramps and reliable, high-quality products. If you’re ready to implement a safe launch for your next project, we’re here to help guide you through the process and ensure a successful outcome. Contact us today to learn more about how we can support your launch and drive operational excellence in your production line.