Easy Strategies to Prevent Defects in Manufacturing
March 18, 2025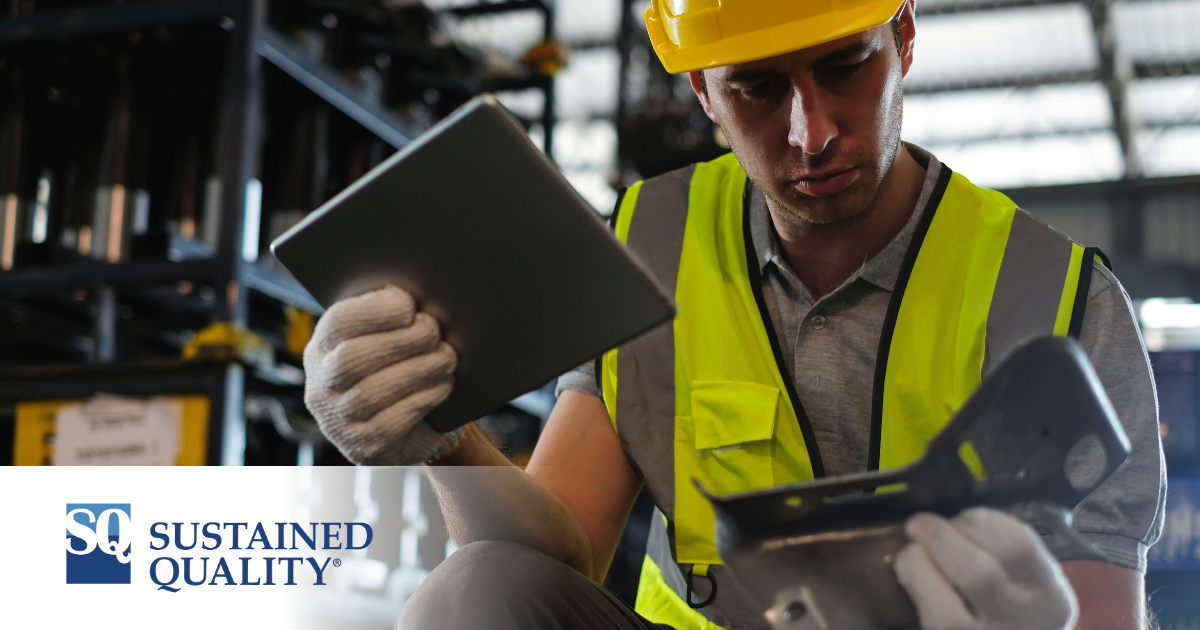
Every manufacturer dreads defects. They slow down production, increase costs, and frustrate customers. But what if you could prevent many, or even most of them, before they even happen?
Defects are a common challenge in manufacturing, appearing in various forms such as design flaws, material inconsistencies, assembly errors, and functional failures. However, with careful planning and effective strategies, manufacturers can significantly reduce defects, leading to higher product quality, lower production costs, and improved customer satisfaction.
We’ll explore the different types of defects that may arise in manufacturing and present practical strategies to mitigate them.
1. Design Pitfalls: When Blueprints Go Wrong
Design defects occur when product blueprints fail to meet the required standards or intended functions. These issues often stem from inadequate planning or unclear design specifications. Design defects can range from minor inconsistencies to critical structural failures.
Prevention Strategies:
- Collaborative Design Reviews: Think of it like a second set of eyes on an important report—getting engineers, designers, and production teams involved early helps catch issues before they become expensive problems.
- Prototyping and Testing: Develop prototypes and conduct rigorous testing to assess real-world performance before finalizing the design.
- Detailed Documentation: Maintain clear and comprehensive design records to ensure consistency and accuracy across production.
- Iterative Improvement: Perfecting a design in one shot is rare—continuous testing and feedback help fine-tune it along the way.
2. When Products Don’t Perform: Fixing Functional Failures
Functional defects arise when a product does not perform as expected, often due to poor manufacturing execution, insufficient testing, or rushed production schedules.
Prevention Strategies:
- Thorough Quality Testing: Put your products through the wringer with functional, stress, and durability tests to expose imperfections and flaws before they reach customers.
- Quality Assurance (QA) Teams: Implement a dedicated QA team to detect and resolve issues early in production.
- Automated Inspection Systems: Utilize AI-powered and sensor-based quality control to spot defects before products leave the factory.
- Clear Product Specifications: Make sure every team is on the same page with well-defined specs—clearer instructions mean fewer mistakes.
3. Bad Materials, Bad Results: Stopping Raw Material Defects at the Source
Manufacturing processes depend on high-quality raw materials. Poor-quality inputs can lead to weakened structures, failures, and increased waste.
Prevention Strategies:
- Supplier Audits and Certifications: Regularly evaluate suppliers and require quality certifications to ensure consistent material standards.
- Material Testing and Inspection: Conduct rigorous material tests to confirm durability and compliance before production.
- Strong Supplier Partnerships: Work with trusted suppliers who consistently deliver quality materials—and build strong relationships to get the best deals.
- Inventory Quality Control: Keep materials in top shape by storing them properly to prevent degradation and ensure usability.
4. Assembly Line Accuracy: Eliminating Errors Before They Happen
Assembly defects occur when components are not properly integrated, often due to human error, inconsistent procedures, or lack of precision in production lines.
Prevention Strategies:
- Standardized Operating Procedures (SOPs): Establish clear assembly guidelines to maintain uniformity across production.
- Employee Training Programs: Keep teams sharp with ongoing training that reinforces precision and cuts down on costly mistakes.
- Checklists and Inspections: Step-by-step checklists and quality checks at every stage help identify issues before they become bigger problems.
- Let robots do the heavy lifting—automated assembly and augmented reality (AR) guidance help reduce errors and boost precision.
5. Lost in Translation: How Miscommunication Leads to Manufacturing Defects
Defects in manufacturing don’t always stem from technical issues—miscommunication between teams can lead to inefficiencies, production delays, and costly mistakes.
Prevention Strategies:
- Regular Production Meetings: Keep teams aligned with daily or weekly check-ins to tackle concerns and stay on track with manufacturing goals.
- Digital Workflow Management: Use platforms like ERP systems to track production progress, task assignments, and quality checkpoints.
- Comprehensive Documentation: Keep detailed records of product specifications, design changes, and production adjustments.
- Encouraging Open Communication: Create a workplace where employees speak up early and small issues can be caught before they turn into big problems.
6. Human Error: The Defect You Can’t Ignore
Even with cutting-edge technology, people still make mistakes—and those mistakes can be costly, often resulting from fatigue, distractions, or inconsistent processes.
Prevention Strategies:
- Workload Management: Smart scheduling helps prevent burnout—well-rested workers make fewer mistakes.
- Cross-Training Programs: Equip workers with diverse skill sets to improve adaptability and reduce knowledge gaps.
- Peer Review and Quality Checks: Encourage employees to double-check work; a second set of eyes can make all the difference.
- Continuous Improvement Initiatives: Promote ongoing learning, skill development, and feedback loops to drive excellence.
Building a Stronger Manufacturing Process Starts Today
Defects in manufacturing can lead to costly delays, wasted materials, and customer dissatisfaction. However, by implementing proactive strategies—such as improving design reviews, strengthening quality control, and leveraging automation—manufacturers can significantly reduce their frequency and enhance efficiency.
The key to reducing defects isn’t just about fixing problems—it’s about preventing them in the first place. By taking a proactive approach, manufacturers can build stronger, more reliable processes that save time and money. At Sustained Quality, we help companies do just that. Ready to tighten up your production line? Learn more about our services here.