Industry Standards and Issues that Counterfeit Electronic Parts are Creating
January 23, 2019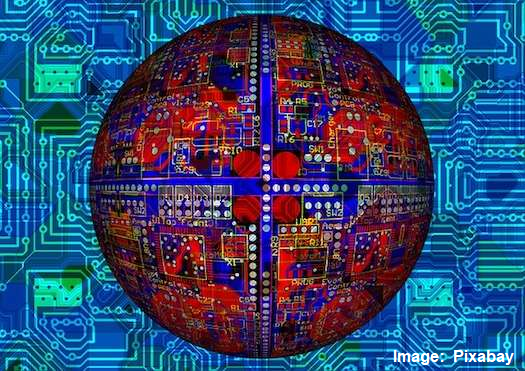
Nearly every industry, purchases electronic components. These parts need to be of the highest quality, especially for applications where safety and reliability are essential, which is why the growing number of counterfeit parts is becoming an enormous concern.
New industry standards may be the answer to preventing the spread of counterfeit parts.
The rise of counterfeit parts
In 2009, NASA came under fire for the use of apparently counterfeit parts in their satellites and spacecraft. While the components were not putting astronauts or satellites at risk, it cost the space agency extra money in testing and quality assurance to make sure the parts met the standards required by NASA and other agencies.
It is important to note that the word “counterfeit” in this context does not mean the same thing it would if the term were applied to money. Counterfeit money is fake. Counterfeit parts are not necessarily fake — they just have not undergone the sometimes expensive safety and quality testing to ensure they meet the specified performance and standards promised by the part. In this realm, the user might be unaware of the origins of the part as well as the quality (specifications, packaging, etc.) of the components.
Thirty years ago, few worried about the problem of fake parts, but, particularly with the globalization of the electronics market, this problem has only grown over the past decade. In 2011, reports indicated that more than half of the electronics distributors in the United States had encountered counterfeit parts. In 2012, a survey conducted by the Senate Armed Services Committee found more than one million counterfeit parts appeared in the Pentagon’s supply chain — and more than 70% of those parts could be traced directly back to manufacturers in China. These components also cost the consumer electronics industry more than $250 billion each year.
As recently as 2017, the United States military estimated that nearly 15% of its supply chain is made up of counterfeit parts.
Continuing improvements to industry standards
Industry groups are working to address the challenge of counterfeit components through standards. SAE International introduced AS5553A in 2009. Later on, in September 2016, the standard was revised and republished (AS5553B). Among other changes, the standard was greatly reduced in length, based on industry feedback that the previous revision was confusingly phrased. The newer revision lost none of its scope. The AS5553 family of standards was designed to help companies avoid, detect and mitigate the damage caused by the introduction of counterfeit parts into a supply chain. The U.S. military adopted this program until 2012.
Then, in 2012, after the report detailing counterfeit parts in the Pentagon’s supply chain came to light, it was apparent that changes were required to improve industry standards and the detection of these potentially unsafe parts. By 2014, the Defense Federal Acquisition Regulation Supplement (DFARS) was in place. This required all defense contractors to have a system in place that can detect and avoid counterfeit electronic parts. Contractors who fail to comply with these standards either face fines or need to replace the questionable parts at their own expense.
These two programs together led to the creation of AS6081, which is still in use today. In 2017, DARPA also introduced the SHIELD program, or Supply Chain Hardware Integrity for Electronics Defense.
Avoiding counterfeit electronic components
All suppliers should adhere to AS5553 and AS6081 standards. Consumers should take time to investigate each supplier’s best practices for preventing counterfeit components from entering the supply chain. “Manufacturers of electronic parts will perform testing as defined by the customer requirement of industry standard, utilize a number of measurement devices (including a DMM), record the data and compile that to create a Certificate of Conformance for that production lot,” said Matthew Boyd, Director of Business Development at NTS Unitek. This will assure customers that the electronic components meet AS5553 and AS6081 standards.
In spite of a growing awareness of the counterfeit parts problem, many industries still lose billions of dollars each year in sales because of fake and low-quality parts. Awareness of the problem is no longer enough. It will take a concerted effort across every impacted industry.
Nichols, Megan. (2019). “Counterfeit Part Prevention Starts with Industry Standards”. Retrieved from https://www.ebnonline.com/author.asp?section_id=4162&doc_id=283794.